Project Description
Car support structure
This case is based on the 2016 Handbook and uses the Qualitative approach
Introduction
The pilot was conducted by the BMW Group and BASF on a polymers support structure for cars produced by BASF and then used in a BMW car. The main goal of the pilot was to identify risks and strengths in the supply chain of the polymers support structure, using the social indicators from the handbook and initiating activities to discuss various topics with different players along the value chain
Application of the methodology
For this pilot, the scales-based approach in combination with a hotspot analysis was used. As the goal of the assessment was to find areas of risks and strengths in the supply chain, the scales-based approach was considered the most fitting to reach this goal.
A cradle-to grave approach was chosen to take into account all life cycle steps of the materials (i.e. extraction of raw materials until end-of-life) and to get insights into the impacts throughout the whole supply chain. The assessment focused on the workers and local community stakeholder groups. The consumers stakeholder group was considered less relevant, because the consumer experience during use phase is not really affected by this component when in use.
After high-level screening, the major hotspots were identified and were further investigated. From the hotspot analysis the following indicators were identified as most relevant for the car support structure supply chain: working hours, training, work-life balance, forced labour, and job satisfaction.
Aggregation was used for some indicators only, since the goal of the pilot was to identify risks and strengths in the supply chain. To achieve this aim, and to define improvement opportunities, non-aggregated results are easier to interpret and give a more transparent overview on of the social impacts along the product life cycle. No weighting factors were used, as the goal of the study was not to generate a single score for the car support structure.
Operationalisation and Feasibility
The sustainability experts from both companies took the lead in this assessment and involved experts from different disciplines and departments. This included the strategy department, the development department and marketing across both companies. Life cycle assessment specialists plus some specific suppliers worked together to collect the data and assess the social impact. Around 3 person-months were needed to collect data and we succeeded in gathering approximately 75% of it. Internal meetings and discussions were organized to involve all parties and to make them aware of the value and benefits of product social impact assessment. Most of the people involved were quite positive and interested in the outcomes of the study. The final results were presented at management level. It was important to show the strengths of this methodology and how it can support management in their decision-making process.
A social database with product or company-related data would greatly reduce workload in the data collection phase. Most of the data for the scales-based approach is available and not confidential, but collecting this data is very time-consuming. The Social Hotspot Database, which is already available, allows us to check some of the topics covered in the handbook. However, a further extension of this database is desirable to cover all indicators of the scales-based and the quantitative approaches proposed in the handbook.
Value added
This pilot gave a clear and comprehensive overview of the social impacts along the whole supply chain. The assessment uncovered unknown hotspots; it identified parts of the life cycle with no or low risks as well as part of the life cycle where no further improvement is needed.
Perceived advantages of using the Product Social Impact Assessment are:
Valuable information about the product and its social impact;
More transparency, trust and better cooperation between customers and suppliers.
Good overview for comparison of different materials and their supply chains.
The handbook gave clear guidance on how to work, how to conduct the impact assessment, which aspects the practitioner should focus on, and in which format the results could be presented and discussed.
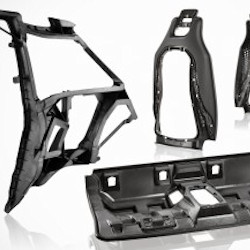