Project Description
Run on Flat
This case is based on the 2016 release of the handbook and explores the Quantitative approach
Introduction
The product chosen for this pilot was a Run On Flat tire as mounted onto a BMW vehicle. This tire is designed to provide extended mobility by providing temporary performance in deflated mode. In order to simplify analysis, four main materials were considered in the production of the tire, with the main raw material feedstock being produced by BASF and the tire manufacturing phase being conducted by Goodyear. This case demonstrates the methodology by evaluating a well-known product and product application. Through the testing, we considered multiple tiers in the supply chain and attempted to collect data through a variety of methods. Furthermore, this case sought to examine how the methodology might be applied to businesses of different sizes.
Application of the Methodology
We decided to implement a quantitative approach for the entire product life cycle while considering all three stakeholders groups. We decided to apply a quantitative approach because BASF, Goodyear and BMW are interested in quantifying social aspects along the supply chain in existing life cycle activities. Examples of experiences in this topic are BASF’s SEEBALANCE® methodology as well as BMW Group´s Sustainability Risk filter. Another goal was to test the ability to quantify and aggregate the data to allow for comparison of alternatives. The test phase was a good opportunity to see if the methodology provides a workable approach to support decision-making with quantified, life cycle-based data founded on social indicators.
Our initial goal was to assess the product from cradle to grave, including the production of raw materials at multiple tiers of suppliers throughout the use phase of the car (the tire can, for example, affect the comfort and “well-being” of the driver in the use phase) until the end of life of the tire. Inadequate data availability led to the eventual exclusion of some phases and a focus on the most relevant products and life cycle steps.
We decided to include data from the production of other materials, such as steel and natural rubber that were outside the operational control of the project partnership. The data were collected using questionnaires to suppliers, different types of reports, and statistical databases. This approach allowed testing of data collection from multiple data source types, showed the quantified contribution of different industries to the social impacts and made it possible to identify improvement potential in the supply chain.
Operationalisation and Feasibility
Operationalisation of the assessment might be easier in large companies because they might have expertise in house. In our case, it was necessary to involve several departments in the assessment (e.g., human resources, company site management, procurement, EHS). Furthermore, the assessment was coordinated by specialists from the departments responsible for sustainability and life cycle assessment who were able to contribute data from existing databases and methodological set ups. These departments may be best suited to facilitate the assessment, particularly a quantitative one, because the logic relies on the methodological approach normally used in a life cycle assessment. Even if there are no existing ISO standards for social assessments, the logic and processes of ISO 14040, 14044, and 14045 are helpful in performing a study using social indicators.
The time requirement is not easy to estimate as it may depend on company size, the number of parties involved in the data collection process, existing databases and data sources. Due to the large number of indicators for which it is necessary to find data, data collection is likely to require a minimum of 30 to 40 working days. This depends to a large extent on the complexity of the assessment, the number of industries covered, and the number of alternatives to be assessed. It is easier if all companies involved in the product life cycle jointly participate in the project; otherwise, obtaining social data may be challenging for reasons of confidentiality.
In our case, we succeeded in obtaining 65% of the data for the entire life cycle. This included steps that were not directly controlled by the project partners. In some cases, we found that it is possible to obtain secondary data from sustainability reports and statistical data at sector or country levels. However, statistical data were not available for all indicators within the assessment (e.g., job satisfaction, experienced well-being). The end-of-life step was particularly challenging: No specific social data were available and it was not even possible to identify country-specific data.
By asking similar questions to different stakeholders about the same area, it was found that interpretation may pose a challenge due to greater subjectivity in the social metrics. More guidance may therefore be required in the future to enable more uniform assessments and to ensure that all actors within the value chain respond similarly to questions. The testing further showed that there were opportunities to improve the quantitative assessment methodology both for indicators and aggregation of results. This feedback was integrated into the revised handbook.
For a number of reasons, some modification would be required for it to be truly applicable to this group: 1) criteria may be worded for an organisation with a management structure and employees (e.g., employment relationships), 2) some criteria may not be expected of small farmers or suppliers, 3) some criteria would require consideration external to a farmer’s operation (e.g., training), 4) some criteria would need to be interpreted differently (e.g., wages), and 5) some data may not be collected or available (e.g., job satisfaction). This experience has also been made in other agricultural applications and initiated the development of “AgBalance™” by BASF, a holistic agriculture specific evaluation method including social indicators.
The results of the analysis can be used in internal decision-making, as well as for marketing purposes by informing the supply chain and society about the benefits related to products and innovations. It makes sense to place priority on evaluating products that have high visibility in society, due to the greater consumer awareness of such products. Social benefits/impacts of a product might help to spread the product itself in the marketplace because of its sustainability performance and generates better understanding of this new type of evaluation including social aspects. Additionally, specific hotspots can be identified and optimized during product design and development and can be shown to different stakeholders. It is also helpful to get an overview of the whole life cycle of a product and supply chain, refine results from important life cycle steps, and identify areas where improvements would be most effective.
Value Added
The methodology helps to identify the most relevant social indicators and impacts, in addition to any data gaps. The transparent data aggregation provides direction for decision-making and can support development processes as well as demonstrate future product improvements. Furthermore, it was found that the data collection process could facilitate discussions with supply chain partners and provided a tool for engagement on important social topics within the company across functional groups. Due to consideration of both positive and negative criteria, the methodology allows for an action-based discussion that may help to promote more positive actions throughout the supply chain. This is a part of a more sustainable product solution that can be supported with quantitative data. Lastly, the methodology facilitates the communication of the social benefits of products to both sustainability professionals and non-experts to support a general understanding of the contributions of products and applications to a more sustainable society.
The pilot showed that the quantitative approach can generate information related to a product’s contribution to society (e.g., how many safety training hours are associated with the production and assembly of a tire throughout its life cycle). These data points are not easily available, but support the understanding of the overall importance of a product and provide a full picture of improvement opportunities beyond environmental and economic aspects in order to generate more sustainable solutions. The quantification allows a very distinct discussion of the results and the efficient support of decision-making processes. If it were to be scaled up, for instance to all produced cars, it could generate information about the overall contributions of specific products to social indicators. If the understanding of the methodology is clear, it might also be very interesting to assess products with lower visibility in order to demonstrate their contribution (positive or negative) to social indicators. The products with mainly positive contributions may in turn lead to higher acceptance of products in society.
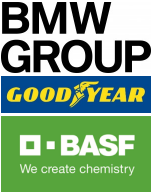
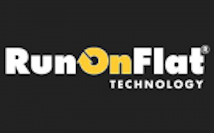