Project Description
Task chair component
This case is based on the 2016 Handbook and uses the Qualitative approach
Introduction
Steelcase and DSM have partnered in this pilot. The product chosen by the companies was a Steelcase task chair component, made of a DSM polyamide grade.
Application of the Methodology
The approach chosen was the “scales-based” assessment. The scope was the life cycle stages from materials production to use phase, with the following actors:
- Materials production: DSM and a DSM supplier
- Component production : injection moulding at a Steelcase supplier
- Assembly and completion of the final product: assembly of the task chair at Steelcase
- Use: consumer
End of life, transportation, and some of the materials production steps were excluded from the scope considering the limitations of the data in terms of time and availability. The consumer’s “experienced well-being” was excluded from the scope.
Operationalisation and Feasibility
Several departments were contacted for the related data collection, depending on the companies involved: human resources, product certification in-house experts, research and innovation, operations, environmental management and sustainability. Most data were available. Test partners considered that this data collection was not very time consuming.
Value added
It sounds obvious that such a social assessment could be performed on most office furniture products (chairs, storages, desks, partitioning walls, screens, etc.). It is also highly probable that the most interesting outputs would come in particular from the analysis of both the materials production stages. In fact, many industrial operations occur during those stages, which means that a number of workers and local communities are potentially directly or indirectly concerned.
Based on the test and discussions following the outcomes, Steelcase and DSM have defined a number of observations and recommendations:
If the assessment is primarily based on reports provided by companies and suppliers themselves, how can the data quality be guaranteed and the right level of confidence regarding the resultant answers (i.e. risk mitigation strategy) be created? Suggestions might include requesting extra evidence that substantiates the answers, or performing audits. Within the boundaries of throughput time and time spent on this pilot, it was difficult to assess the end-of-life stage. For future case studies we would recommend creating a database with end-of-life principles and data.
For this test we looked at one part of an office chair. The question is how to allocate the social impacts of a whole chair which could consist of a large number of components. A chair is made from about 300-400 parts, of various weights (from a few grams to a few kilos) and material types. We believe it is important to continue exchanges between participants to find a feasible and practical solution for this.
We believe that data collection could probably be optimized if data are collected together with environmental data, for instance for LCAs, certifications, CSR reports, etc.
Product Social Impact Assessments can provide additional data that can be used for CSR communications, except that with this type of assessment there is a more important focus on specific products and/or specific life cycle stages (e.g. external production).
Assessments like this can potentially create new information that can be used in marketing, for instance new information on improved experienced well-being by the end-user (including, for instance, comfort). In this case we could not test this, but we can imagine that if you assess a whole product, market research can help to provide information on experienced well-being.
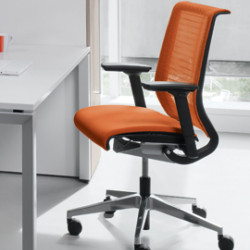